10 Easy Facts About Alcast Company Shown
10 Easy Facts About Alcast Company Shown
Blog Article
What Does Alcast Company Mean?
Table of ContentsThe Definitive Guide for Alcast CompanyThe Single Strategy To Use For Alcast CompanyA Biased View of Alcast CompanyThe smart Trick of Alcast Company That Nobody is DiscussingThe Single Strategy To Use For Alcast CompanyNot known Factual Statements About Alcast Company
The subtle distinction exists in the chemical web content. Chemical Comparison of Cast Light weight aluminum Alloys Silicon promotes castability by reducing the alloy's melting temperature and boosting fluidness throughout spreading. It plays an important duty in enabling complex mold and mildews to be filled up accurately. Additionally, silicon contributes to the alloy's toughness and put on resistance, making it important in applications where resilience is essential, such as auto components and engine elements.It likewise boosts the machinability of the alloy, making it less complicated to process into completed products. This way, iron adds to the total workability of light weight aluminum alloys. Copper raises electrical conductivity, making it useful in electric applications. It likewise boosts deterioration resistance and contributes to the alloy's overall stamina.
Manganese adds to the stamina of aluminum alloys and enhances workability (aluminum foundry). It is commonly utilized in wrought light weight aluminum items like sheets, extrusions, and profiles. The presence of manganese help in the alloy's formability and resistance to fracturing during construction procedures. Magnesium is a lightweight element that provides strength and effect resistance to aluminum alloys.
The Single Strategy To Use For Alcast Company
It allows the manufacturing of lightweight parts with excellent mechanical buildings. Zinc enhances the castability of aluminum alloys and aids control the solidification procedure throughout casting. It boosts the alloy's strength and solidity. It is typically discovered in applications where complex shapes and fine details are necessary, such as ornamental castings and particular vehicle parts.
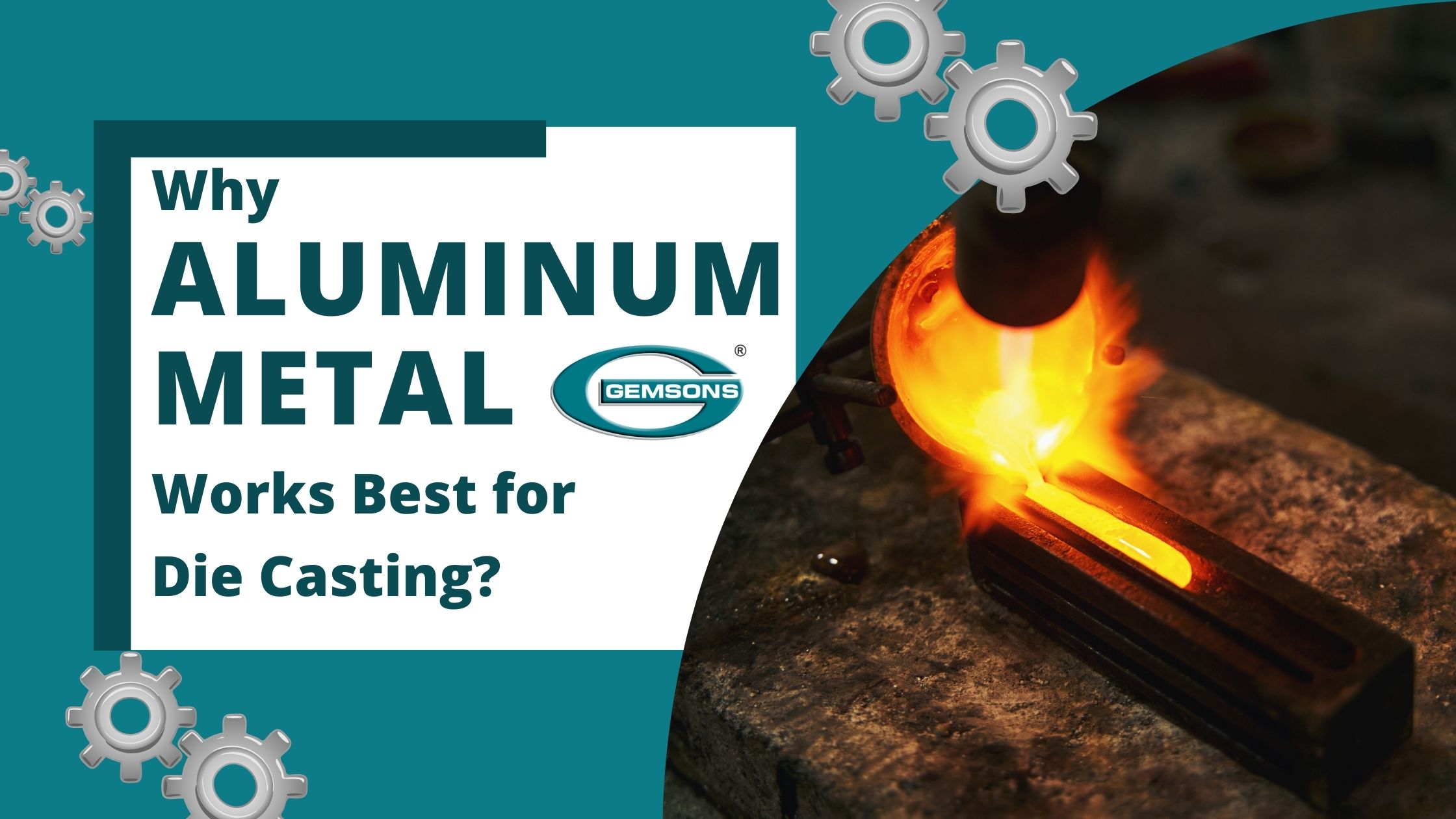
The primary thermal conductivity, tensile strength, return strength, and elongation differ. Among the above alloys, A356 has the highest possible thermal conductivity, and A380 and ADC12 have the least expensive.
Alcast Company for Beginners
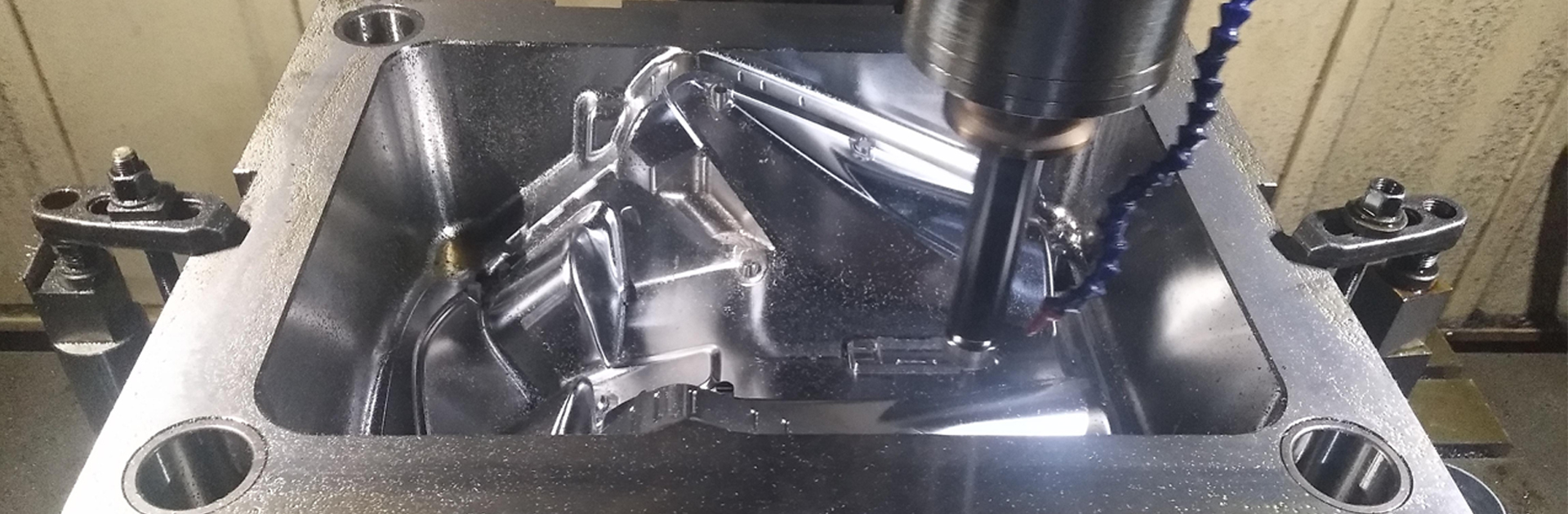
Its distinct homes make A360 a useful choice for accuracy casting in these sectors, improving product resilience and quality. Light weight aluminum alloy 380, or A380, is a widely utilized spreading alloy with several unique characteristics. It offers exceptional castability, making it a suitable choice for accuracy casting. A380 shows good fluidness when molten, making sure detailed and comprehensive mold and content mildews are accurately reproduced.
In precision casting, aluminum 413 radiates in the Consumer Electronics and Power Tools markets. This alloy's exceptional corrosion resistance makes it an excellent choice for outside applications, making sure resilient, long lasting items in the mentioned sectors.
Getting The Alcast Company To Work
When you have actually made a decision that the aluminum die casting procedure appropriates for your project, a vital next action is picking one of the most ideal alloy. The light weight aluminum alloy you pick will significantly affect both the spreading process and the homes of the end product. As a result of this, you have to make your choice carefully and take an educated approach.
Identifying one of the most appropriate light weight aluminum alloy for your application will certainly mean evaluating a vast range of qualities. These relative alloy features follow the North American Die Casting Association's guidelines, and we have actually separated them into two groups. The initial category addresses alloy features that influence the production procedure. The 2nd covers features influencing the buildings of the final product.
Little Known Facts About Alcast Company.
The alloy you choose for die casting directly affects several facets of the spreading procedure, like exactly how easy the alloy is to collaborate with and if it is vulnerable to casting flaws. Warm breaking, additionally called solidification cracking, is a common die casting problem for light weight aluminum alloys that can result in interior or surface-level splits or cracks.
Certain light weight aluminum alloys are extra susceptible to hot cracking than others, and your choice must consider this. Another typical issue located in the die casting of light weight aluminum is die soldering, which is when the cast adheres to the die wall surfaces and makes ejection tough. It can damage both the actors and the die, so you should try to find alloys with high anti-soldering properties.
Corrosion resistance, which is already a noteworthy feature of light weight aluminum, can differ significantly from alloy to alloy and is a vital characteristic to take into consideration depending on the ecological conditions your item will certainly be subjected to (Casting Foundry). Use resistance is an additional building typically sought in light weight aluminum products and can set apart some alloys
Report this page